Progress is progress, right?
After getting the power feeds on the mill back together I aligned the Kurt vise and installed the "V" groove jaw. I put a micrometer on the "V" to make sure it was perpendicular and it was spot-on. Good stuff!
Once I had given it some thought (not like I didn't have enough time

) I decided to use a Starrett edge finder to roughly get the cylinder centered on the quill. I used the hole left by the center drill/live center when I turned them on the lathe.
[Side note: Feel free to enlighten me as I haven't read it anywhere but, is the purpose of the pointed end on the edge finder used to align the quill on a punch mark?] I then went back and used an indicator on the Indicol system to ensure that the cylinder was properly centered.
I had some extra brass shim material sitting around that I slipped in to keep the cylinders from being scored by the sides of the "V".
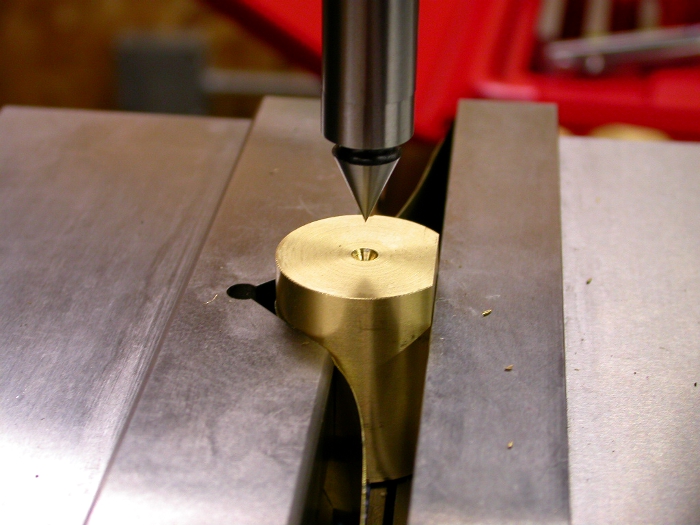
I followed that up with a nice new carbide center drill. I then sacrificed an old 1/8" drill bit and ground it's cutting edges down to 0 degrees so it wouldn't bite into the brass and pull the bit out of the chuck. To keep things as rigid as possible I locked the quill on the mill and raised the knee to drill out the pilot hole. Lots of cranking going on.

The "hole within a hole" that you see is still the leftover from the lathe center as the pic I took of the pilot hole didn't come out well enough to publish.
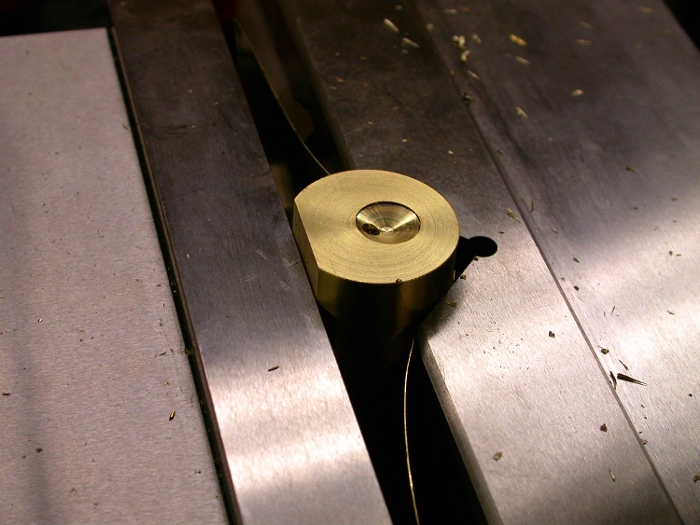
It's at this point that I came to an abrupt halt as I had neither an old (still decent) 3/8" or 5/16" drill bit to re-purpose for brass. I'll have to see what I've got around the house once I get back there this evening.
It may not seem like I did a whole lot but I did run into a nasty little issue that slowed me down for a bit.
I had recently bought a cheap set of R8 collets of unknown asian manufacture. Overall they don't look too bad but I still should have been a bit more careful. The first couple of them I put in the quill using the power draw bar went just fine but I grabbed one I hadn't used before, did a quick visual inspection of the threads and hit the button to screw it in. It went in about 1/4" and locked up tight. I ended up using an adjustable crescent wrench as kind of a "pickle fork" and with the light application of a dead-blow hammer finally was able to get it out of the quill. Looking at the aftermath I could see that the threads were less than ideal and had some rust built up in them just below the 1/4" mark. Once the "primal rage" died down a bit I got out my tap set, figured out the threads, and tapped the collet out properly. On subsequent tries the collet loaded up as slick as could be.
I have another gun show to hit this weekend but I expect I'll be back in the shop and maybe even get a cylinder or two turned out.
Regards,
-Ron